Home / Tool Mold Design & Manufacture
Tool Mold Design & Manufacture
Professional IMD Manufacture
Initial Product Design
Packaging
Kitting
Printing
Machining
Single-cavity mold
- Better control over the molding process and quality of the part.
- Useful for producing larger or more complex parts that require more time to cool and solidify.
- More flexibility to make adjustments to the mold design or material during production.
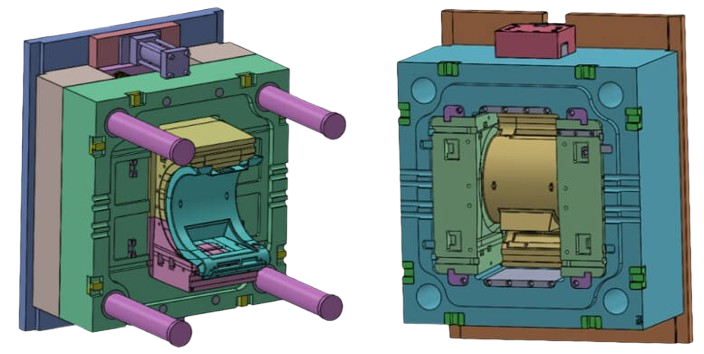
Muili-cavity mold
- Higher production efficiency, as multiple parts can be produced in a single molding cycle.
- Lower cost per part, as the cost of the mold can be spread across multiple parts.
- Useful for producing smaller, simpler parts that require less time to cool and solidify.
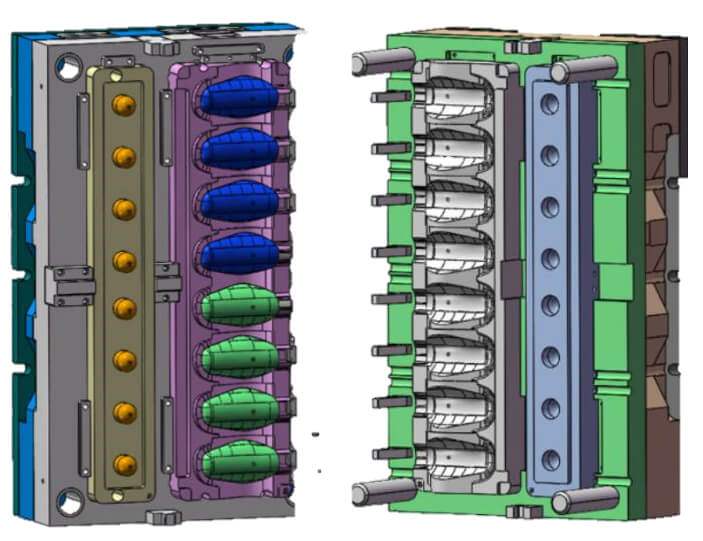
Double-shot mold
- Multi-color plastic injection molding has a wide range of applications in various industries.
- One of the most common applications is in the automotive industry, where multicolor parts are used in car interiors, exteriors, and lighting systems.
- Overall, multi-color plastic injection molding has become a critical technology in many industries, where the demand for high-quality, visually appealing, and innovative products is increasing.
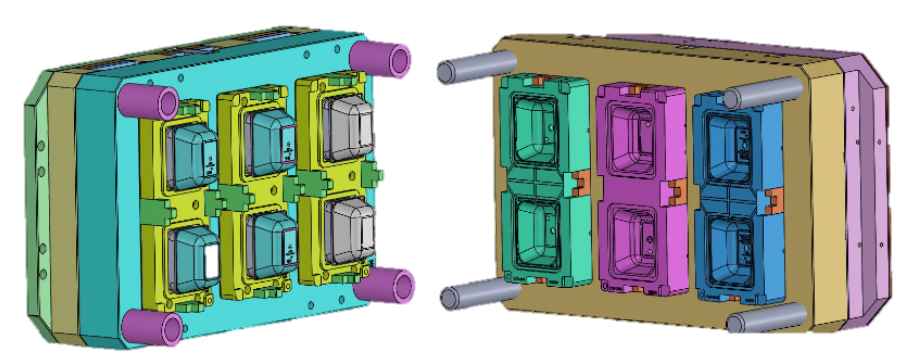
Insert mold
1.Reduction in Assembly Cost
It eliminates post-molding assembly and separate parts installation.
2.Reduction in Size and Weight
It eliminates the need for connectors and fasteners, thereby delivering components that are lighter and smaller.
3.Increased Design Flexibility
Insert molding allows an unlimited number of configurations.
4.Increases Design Reliability
It prevents design problems like misalignment, improper terminations, and others , thereby improving the part’s reliability.
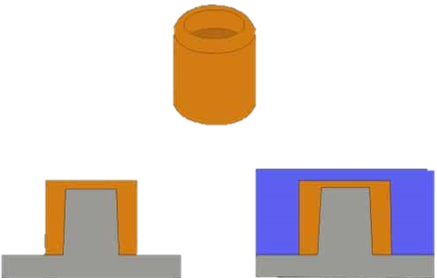
Family mold
1.Lower mold cost
with family molds, there is the need to produce and maintain only one mold tool, rather than several.
2.Low-volume production potential
Family injection molds are the ideal solution for low-volume orders.
3.Improves production rate and cost-per-part
With a family mold, you gain the capability of producing your plastic parts in sets. This also improves your time to market.
4.Ideal for prototyping use
Using this kind of mold helps speed up the design and modification phases, and cuts down on pre-production costs.
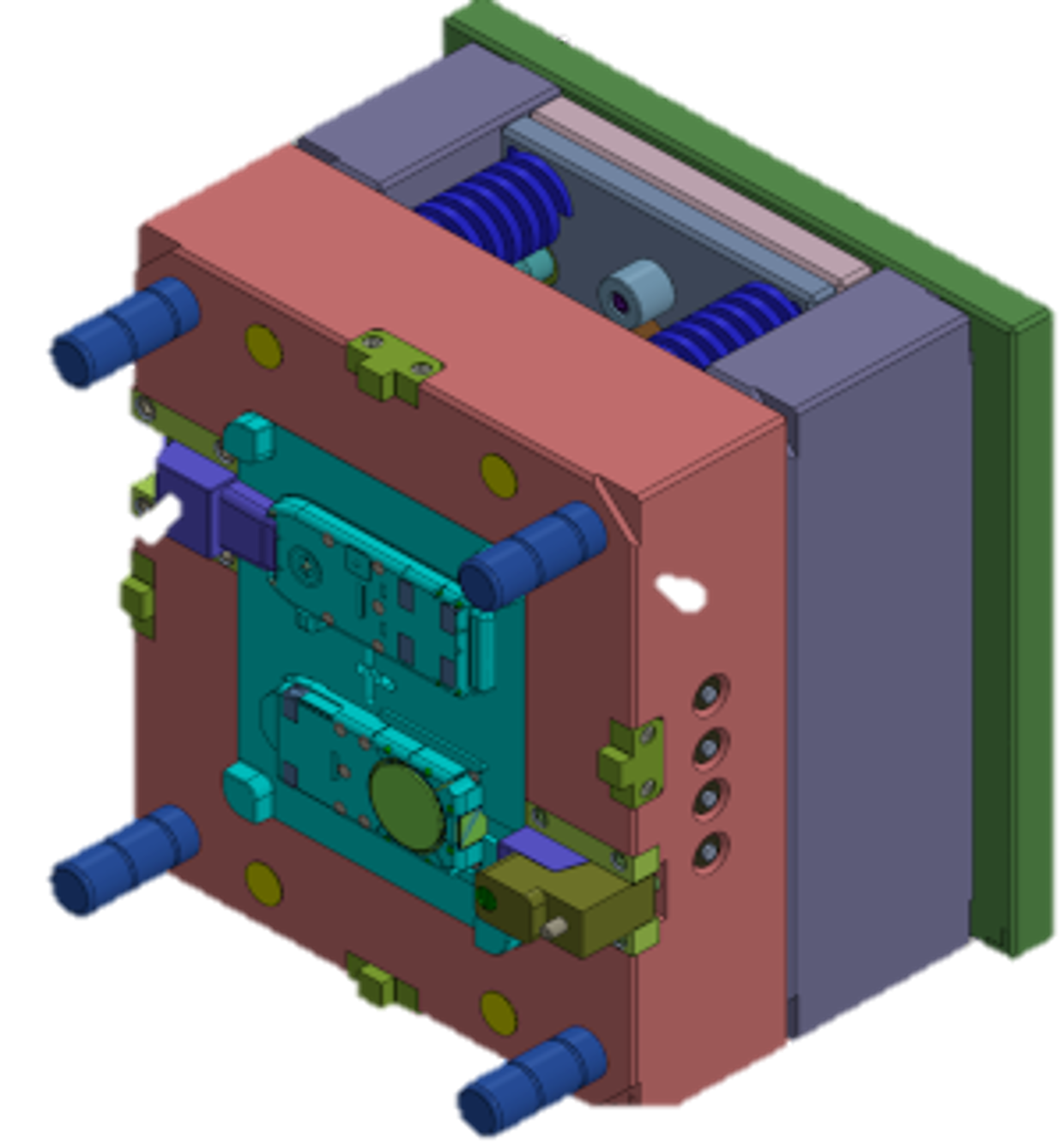
Stack mold
- Reduce the need for multiple molds and multiple presses.
- Enable all parts in all layers to be molded in one shot.
- Allow molded parts to have different geometries, sizes, and fill rates.
- Increase mold throughput.
- Speed up molding cycle times.
- Deliver immediate and exponential cost savings.
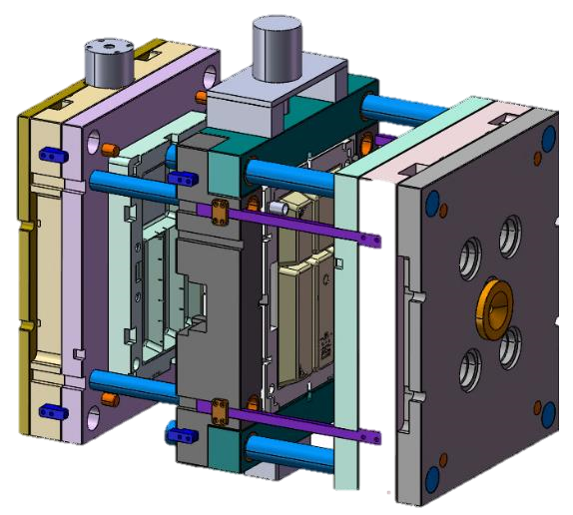
Gas-assisted mold
- It can be the key to obtaining a superior surface finish on your workpiece.
- It reduces the amount of material needed to produce parts and lessening overall part size.
- It has the potential to dramatically enhance structural integrity in parts subject to high levels of stress or load.
- Through gas-injection molding, the strength and durability of a finished product are significantly improved
- It offers a wealth of advantages and is much more eco-friendly than traditional methods.
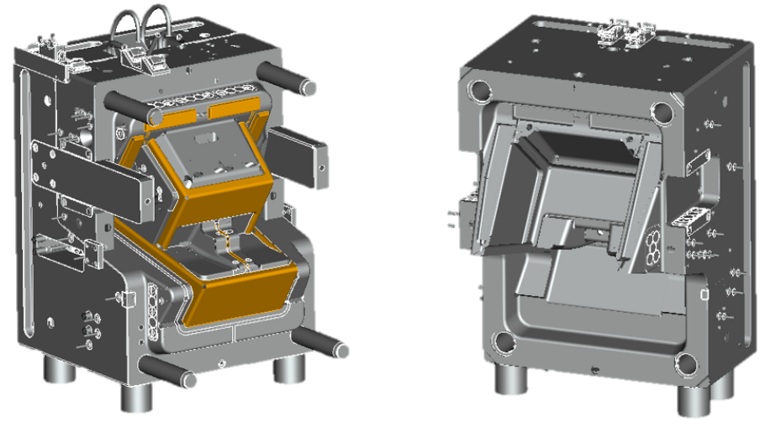
More Products